Previous | Next | Contents
ESDEP WG 3
FABRICATION AND ERECTION
Lecture 3.2.1: Erection I
OBJECTIVE/SCOPE
To give undergraduates, young engineers and managers an introduction to the trade of steel erection.
PREREQUISITES
None are essential.
The following lectures might be helpful:
Lectures 3.1: General Fabrication of Steel Structures
Lecture 3.3: Principles of Welding
Lecture 3.4: Welding Processes
RELATED LECTURES
Lecture 3.2.2: Erection II
Lecture 3.2.3: Erection III
Lecture 3.5: Fabrication/Erection of Buildings
Lecture 15A.8: Offshore: Fabrication
Lecture 15B.12: Introduction to Bridge Construction
SUMMARY
The lecture emphasizes the importance of considering erection during all phases of the project. It outlines the principal requirements for a technical specification and also deals with the organisational aspects on site.
It is important that the erection of the steelwork is considered from the very first stages of a project. Both design engineer and fabricator must consider the following:
- Connections on site:
site joints should be bolted rather than welded.
- Preassembly:
the fabricator should limit the number of site splices to that consistent with minimum project cost. The size and weight of structural steel assemblies will be limited by site and shop capabilities, the permissible weight and clearance dimensions of available transportation and the site conditions.
- Dimensions:
all measurements necessary for site assembly should be shown on the drawings.
- Planning:
the sequence of erection should be considered as an integral part of the project process and should be established and documented at an early stage.
- Marking:
the marking of all parts should be clear and consistent throughout the project.
- Resources:
depending on how the site assembly is carried out, it is essential to ensure that appropriate resources will be available.
The erection team on site must ensure that :
- the workforce are aware of and implement the relevant standards and regulations.
- changes in procedures, which become necessary during the erection stages are agreed by the Engineer, and that the technical documents are corrected in order to be consistent.
- hoisting equipment of suitable capacity is available for any preassemblies which must be lifted.
- means of access, such as scaffolding stairs and platforms, are installed to enable bolting and welding to be carried out satisfactorily.
Erection of structural steelwork is, therefore, an activity that requires detailed consideration from both an engineering design and organisational point of view. Sections 2 and 3 of this lecture
discuss these matters under the headings of: Technical Specification and Site Organisation.
The Technical Specification for Erection should be developed as early as possible and should outline the conditions required on site and the technical standards in force. The documentation should deal with the following matters:
- Basic sequence of erection.
- Specification for erection, (see below).
- Standards in force.
- Organization on site.
- Basic site accommodation.
- Man-hours estimation.
- Erection personnel.
- Main plant and erection tools.
- Erection plan.
- Erection drawing.
- Safety programme.
- Quality Control programme.
Specification for Erection
The specification for erection should include, in as much detail as possible, the following information:
- Requirements for unloading, storage, and handling.
- Details of any preassembly required on site.
- Dimensional and levelling tolerances, including those required for foundations and baseplates.
- Specification for activities relating to the assembly itself such as bolting, welding and testing.
The site organisation required depends largely on the size of contract; in the case of a major project it could, for example, be subdivided into the following sections:
- Technical Office.
- Scheduling and Planning.
- Implementation and Production.
- Administration.
- Safety.
- Quality Control.
- Social Management.
Figure 1 gives an example of an Organisation Chart for the extreme case of a project for the erection of a large steel frame. The chart is applicable to a direct assembly workforce of approximately 125 men.
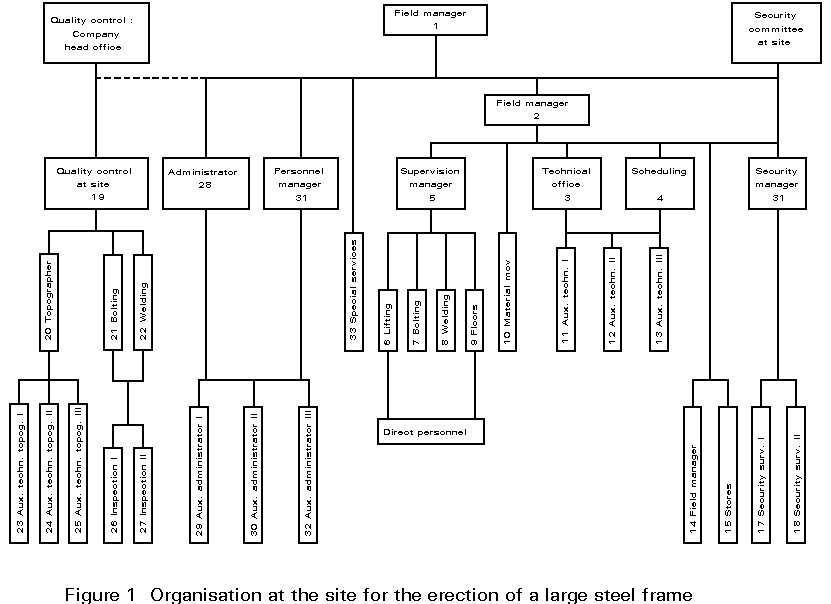
The Erector must have adequate facilities available on site for his personnel, including appropriate office accommodation, sanitary services and storage areas. He must also ensure that the site is properly supplied with mechanical services necessary for erection such as electricity, gas, compressed air, etc. These facilities and installations must comply with the following requirements:
- They should be situated, where possible, in close proximity to the work site, giving easy access to the site without interfering in any way with the progress of the work;
- They should be adequately constructed to, at least, the minimum legal requirements;
- They should have communication facilities;
- They must be maintained in satisfactory condition throughout the work and removed on its completion.
It is essential to estimate the direct manpower resources required in order to properly programme the erection process and accurately forecast the time of completion and the costs incurred.
Manpower resources are normally estimated by calculating the number of direct man-hours required in steel frame erection. An adequate estimate can be obtained based on the erection weight broken down item by item (columns, beams, bracings, floors, etc.), and applying various weight rates (in hours) obtained from past experience.
For a more accurate estimate, each activity can be evaluated, not only in terms of its duration, but also in terms of personnel required to complete it. The product of the time (in hours) multiplied by the number of people in the team will give the man hours for each activity which can be totalled to give the direct man-hours required for the whole job.
Once the activities involved in the erection have been decided, the tools and equipment required to carry out the work can be defined; these may include:
- Cranes of various types.
- Transport equipment.
- Special erection equipment, such as erection masts, erection bridges, etc.
- Winches (electric and pneumatic).
- Bolting equipment, such as spanners, ratchet spanners, torque wrenches, torque testing equipment etc.
- Welding equipment including cables, guns and drying ovens.
- Air compressors.
- Electric generators.
- Hydraulic jacks.
- Measuring equipment such as theodolite, levels, tapes, and laser equipment.
- Miscellaneous equipment such as pulleys, spreader beams, etc..
- Wire ropes, hoisting slings, shackles, etc..
- Handling tools.
The heaviest or highest element to be erected, or the part which requires the greatest lifting capacity (radius-weight) determines the minimum crane capacity to be used.
Figure 2 shows the various lifting capacities of a tower crane.
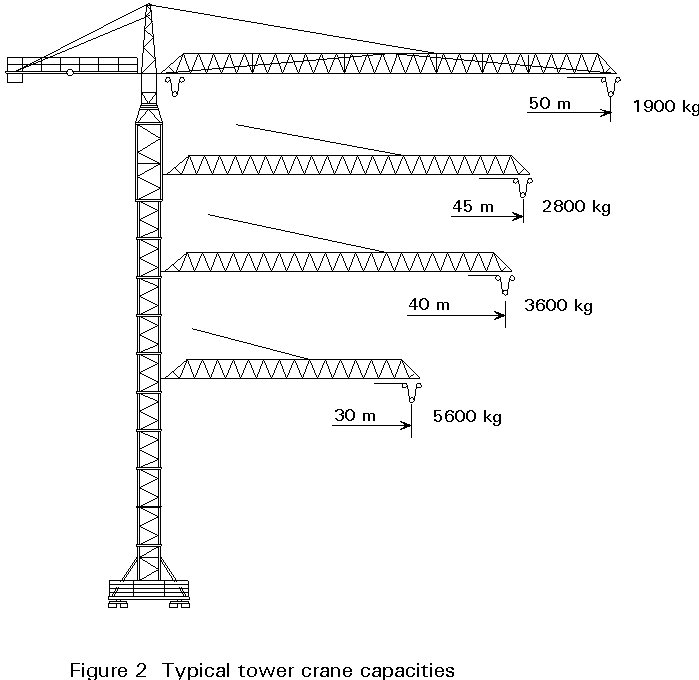
- Erection requirements should be considered at the earliest stages of the project, by both Engineer and Fabricator.
- The Technical Specification for Erection should outline the conditions required on site and the technical standards in force; it should also give a detailed description of how the structure is to be erected, i.e. unloading, preassembly, tolerances, connections, etc.
- The site organisation must be carefully considered in terms of the requirements for manpower, tools and site facilities and service installations.
- Arch, H., Erection, Chapters 33 - Steel Designers' Manual, Oxford, Blackwell Scientific Publications, 1992.
- Thornton, W. A., "Design for Cost Effective Fabrication and Construction", Chapter 7.1 Constructional Steel Design, London, Elsevier Applied Science, 1992.
- Miller, E. W., "Erection of Steel Structures", Chapter 7.2 Construction Steel Design, London, Elsevier Applied Science, 1992.
- Potter, P. D., "Fast Steel Erection": Steel Fabrication Journal, No. 46, February 1983, Australian Institute of Steel Construction.
- The Steel Construction Industry Code of Practice for Sage Erection of Building Steelwork: Part 2 - Multi-storey Buildings and Structures, Australia, Australian Institute of Steel Construction, 1989.
- Eurocode 3: "Design of Steel Structures" ENV 1993-1-1: Part 1.1: General Rules and Rules for Buildings, CEN, 1992.
Previous | Next | Contents